

From there it kind of snowballed from one client to the next. At one point I was talking to an old acquaintance about looking for new opportunities and he told me he needed help ASAP so a week or two later I was on a plane to visit a factory for him. I built the company partially out of necessity, partially out of happenstance. The whole mechanical engineering gamut! I also do a little industrial design and electronics engineering but it’s more of a supplement to my mechanical engineering work. I do CAD, 3D printing, physical prototyping with assembly, testing, analysis, documentation, and factory management. For some clients, that’s been early stage concepting and design, for other clients, that’s been later stage smoothing out production bottlenecks. I help out in those crunch phases to iron out whatever problem they’re having. The hardware development cycle happens in fits and starts, crunch and lull. I founded Measure Twice Labs to help early-stage hardware companies take the next step in their development process. I was used to uniform strength but had to adapt to figure out part orientation to accommodate for FDM 3D printed plastic being very weak in the Z direction.Ĭould you explain furthermore what Measure Twice Labs is and the services that you are providing? After my first couple pieces snapped, I learned pretty quickly that DFM (design for manufacturing) for 3D printing was quite different than traditional subtractive manufacturing in metals and carbides.
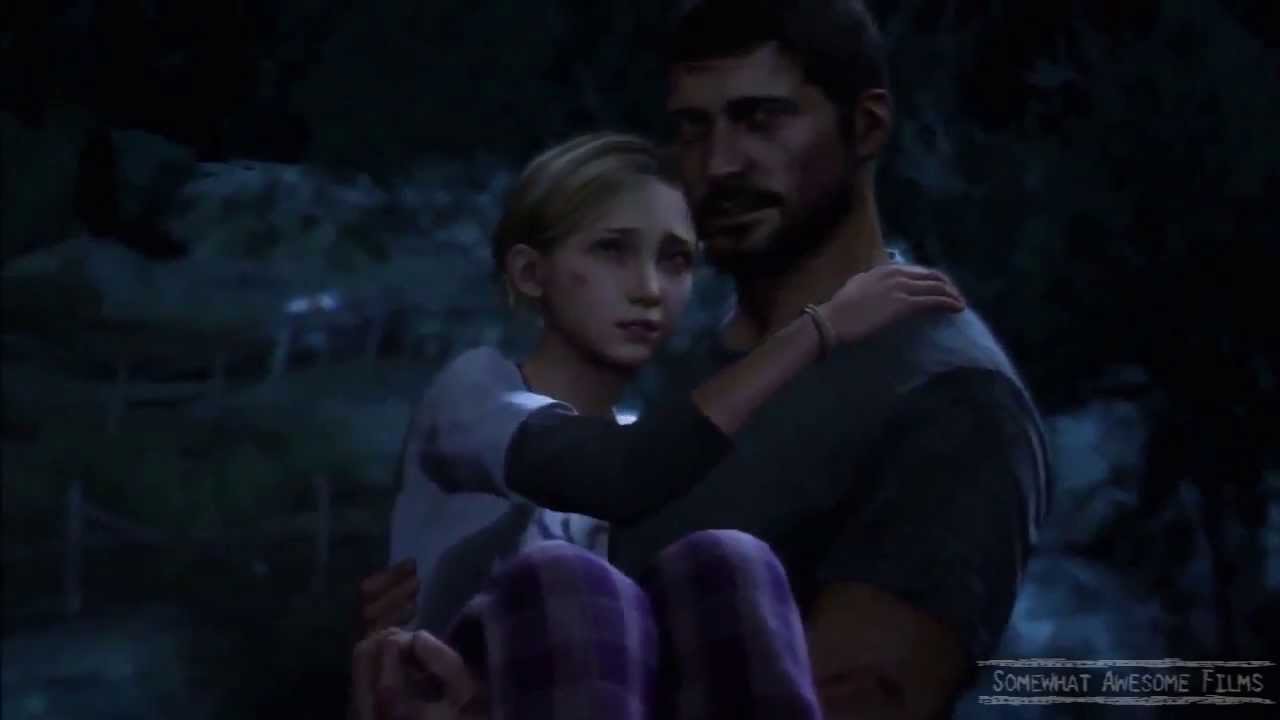
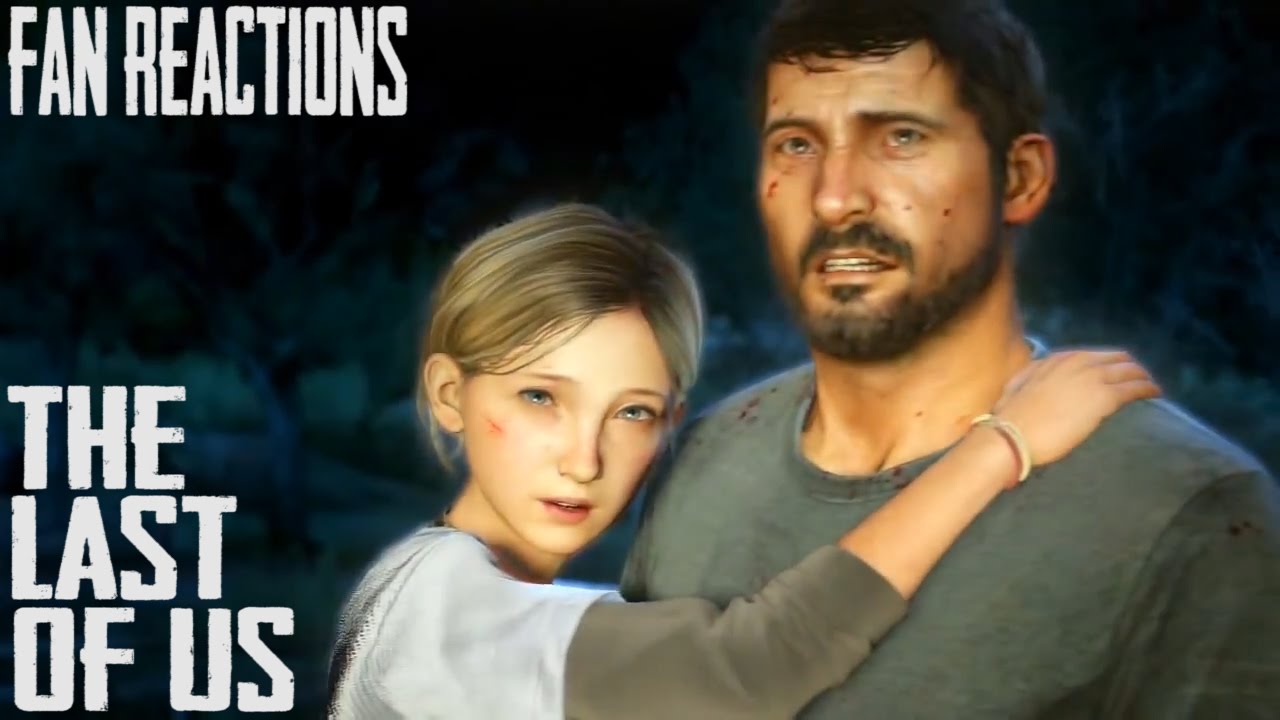
It was a little fussy but a good machine to learn on. We had an in-house Makerbot Replicatior 2. Basically mocked up some simple blocks with threaded inserts for screws as well as holding clips. I started by designing a couple of smallholding fixtures for testing assemblies. I joined a new company and a big part of my job was prototyping so I had to get good fast. My first experience 3D printing was at work. What was your very first experience with 3D Printing? Most of what I print are prototype parts for companies I work for, as well as for my own products that I’m working on. Nowadays 3D printing is a big part of my job.
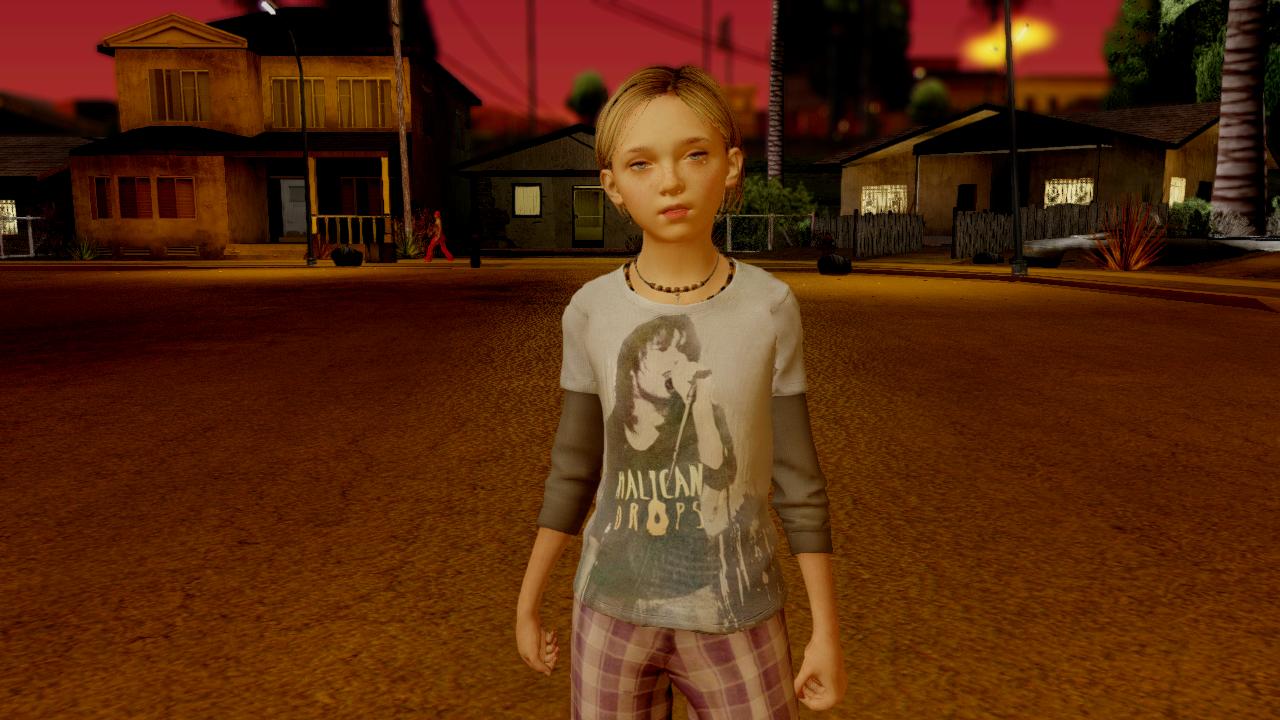
My first job out of school was working on relatively low volume industrial equipment so most of my early work was designing for traditional subtractive manufacturing (lathe, mill, wire EDM). 3D printing wasn’t as prevalent then as it is now. I graduated with a bachelors degree in mechanical engineering from Worcester Polytechnic Institute in 2006. I’m a consulting mechanical engineer living in New York City. Sarah, could you let us know about your background and what brought you to 3D printing in the first place? Sarah Pavis is the Founder and Principal Engineer at Measure Twice Labs, a New York City-based mechanical engineering design and consulting studio.
